ESG Economist - Energy-intensive industry: from less gas to more electrification
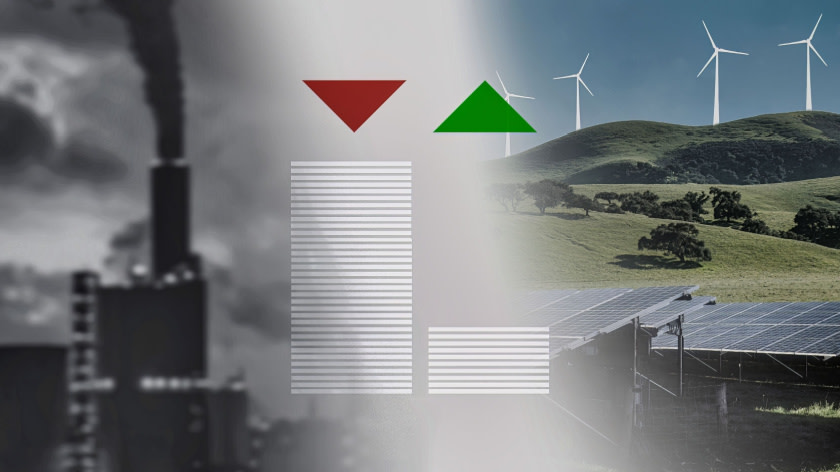
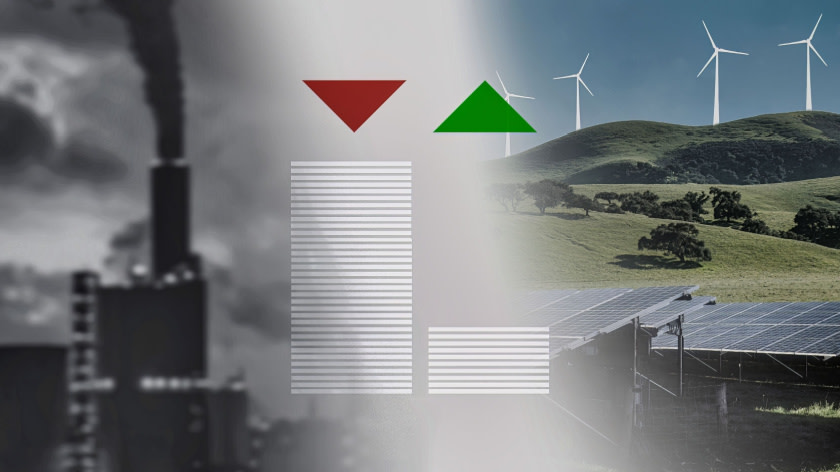
Highly energy-intensive industrial subsectors account for 90% of total industry energy consumption. Compared to the less energy-intensive industrial subsectors, the highly energy-intensive companies in industry have been hit much harder by the strong rise in energy prices recently. The moment electrification in industry also gets more traction in the coming years, this is going to benefit sustainability.
Many energy-intensive industries are under increasing pressure to reduce their carbon footprint. In the climate crisis a lot of attention is focussed on the most energy-intensive sectors and the climate measures taken there. After all, energy-intensive sectors are still highly dependent on gas and also responsible for a large share of greenhouse gas emissions. More electrification, but also taking steps in energy efficiency is going to help the energy-intensive companies reduce energy consumption and GHG emissions. But less energy-intensive industrial sectors also need to stay engaged with the path to carbon neutrality. In this analysis, we investigate the energy consumption and GHG emissions trends of the low, medium and high energy-intensive industries in the Netherlands and provide insights with regards to for future investments.
Energy-intensive sectors in industry
The following industries are considered highly energy-intensive in this analysis: food, paper, building materials, basic metal and chemical industries. In addition, we distinguish medium energy-intensive industries and low energy-intensive ones, see also the below figure on the right hand side. When calculating the energy intensity of these sectors, we plot the amount of energy consumed (in Peta Joule, PJ) against the sector's added value. A decrease in energy intensity indicates that, on balance, less energy was used to produce a product or service. For example, energy intensity in industry as a whole has decreased by 32% over the past decade. This indicates that the energy efficiency of industrial processes has increased. An additional benefit is that this improvement has also reduced greenhouse gas (GHG) emissions and GHG intensity.
The GHG emission intensity - this is the total amount of CO2-eq. in kg related to value added - has decreased by 28% over the same period. The average energy intensity of the whole industry is largely driven by the chemicals industry. This subsector pulls the average for the industry as a whole up considerably. In GHG intensity, both the chemical industry and the basic metals industry have a large share.
The impact of highly energy-intensive industry is high, both in terms of final energy consumption and greenhouse gas emissions. Collectively, the highly energy-intensive subsectors account for about 90% of total energy consumption in industry, while they also have a 94% share of total industrial GHG emissions. These subsectors are thus pre-eminently the sectors to monitor in terms of trends in energy consumption and GHG emissions, but especially whether they are taking measures that would move the needle in terms of their carbon footprint.
More (or less) energy consumption leads to an increase (or decrease) in GHG emissions. The two magnitudes are closely linked and broadly run almost in parallel over time. In the base metal industry, energy consumption fell more sharply from 2012 to 2014 due to the bankruptcy of a major aluminium smelter. However, GHG emissions remained relatively high due to the fact that the bulk of GHG emissions come from the steel industry in this sector.
Energy is used in energy-intensive industrial sectors for a wide range of purposes. This can be for industrial processes and product assembly, as well as steam generation and cogeneration. In addition, much energy is also used for process heating and process cooling, heating and air conditioning for buildings and, of course, lighting. However, the energy use of the industrial sector can also relate to basic chemical raw materials, where the energy carrier is incorporated into finished products.
Companies can reduce energy consumption in a number of ways. Here, energy efficiency plays an important role. Once processes are screened in terms of energy consumption and when different processes are better coordinated, energy wastage can be better prevented at an earlier stage. For instance, energy lost in processes (in many cases this is heat) can then be recovered and used elsewhere (internally or externally). Greater use of combined heat and power (CHP) can also improve efficiency, in which a fuel (often a gas variant) generates both electricity and heat. Finally, more use can also be made of secondary raw materials in the production process. Processing these instead of primary raw materials requires much less energy. Especially in the metal sector, a lot of energy gains can be made from this.
Impact energy crisis
Highly energy-intensive industrial companies have been hit harder by energy price developments than companies in the less energy-intensive subsectors. The producer price index increased much more strongly in the highly energy-intensive industrial sectors, while production in this segment showed a stronger contraction. In terms of gas consumption of the highly energy-intensive industries, a clear drop in gas usage can be seen after Russia's invasion of Ukraine (February 2022).
The relatively high gas prices have been a strong incentive for many companies to rapidly reduce gas consumption. Efficiency measures, electrification (such as heat pumps and electric boilers) and fuel substitution (in particular, more use of petroleum products) made it possible to reduce gas consumption in the short term. Sometimes, however, the crisis meant that production lines had to be temporarily or completely discontinued. The average energy-intensive industry shows a strong increase in production, which is mainly due to strong growth in the machinery industry in the Netherlands.
Reducing greenhouse gas emissions
Several exogenous shocks have strongly influenced the industry's GHG reduction trend in recent years. Economic downturns (such as in 1999 the internet bubble, in 2008-2009 the major financial crisis, from 2020 the Covid-19 pandemic and from 2021 the energy crisis) and also economic prosperity have had positive and negative impacts on industrial GHG emissions, respectively. Over the entire period 1990-2022, industrial GHG emissions were reduced by an average of 34%, mainly due to measures in the very high and low energy intensive industries.
The medium energy intensive industry has been able to reduce GHG emissions to a much lesser extent and therefore has a much bigger task ahead towards 2030. The success of emission reduction towards 2030 will be determined by the climate measures that the highly energy-intensive industry will take. This segment includes many companies that fall under the EU ETS (emissions trading system) and are therefore more forced to take action. Here, more energy efficiency and electrification are the key spearheads.
Electrification as the holy grail in industry
In recent years, investments in projects such as solar and wind farms have taken off and, as a result, the production of electricity by wind and solar power has increased more strongly. The share of renewable in electricity production is going to increase further. In the Climate Accord, for instance, it was agreed that by 2030 the share of renewable electricity in total electricity production should be 70% and that by 2035 the Netherlands should have an almost 100% carbon-neutral electricity sector, according to the draft Integral National Energy and Climate Plan of June 2022. The moment electrification in industry also gets more traction in the coming years, this is going to benefit sustainability. But this never runs one-to-one. For some industrial processes, electrification can be relatively easy to achieve, but for other industrial sectors (such as in the steel industry), replacing fossil fuels with electricity is a more complex task, which will take years to implement.
Electrification in industrial companies has several advantages. Not only is electrically driven equipment slightly more energy-efficient, but maintenance costs are often lower. And in addition, greenhouse gas emissions fall, the moment the electricity used is low-carbon. However, the heterogeneity of the industrial sector - due to the wide variety of production processes and different levels of energy consumption - increases the complexity towards full electrification in the sector. A 100% electrified industry is therefore not realistic in the short term. Moreover, it would put too great a strain on existing grid capacity. A good connection to the electricity grid with sufficient capacity therefore remains an important precondition for further electrification in industry. Here, the government has an important directing role. Through policy, subsidies, targeted investments, but also through education and knowledge sharing, it can provide the necessary stimulus for the transition to more electrification.